Among several categories of Additive Manufacturing processes, Laser Metal Deposition (LMD) is suitable for producing complex geometries and optimized shapes. This technique emerged in modern industry (e.g., aeronautics, automotion, biomedics) as one of the most important manufacturing technology. In particular, LMD process is based on the heating and melting of a substrate due to a direct energy source, as well as on the simultaneous melting of powder material deposited on the substrate. The big challenge is to reproduce the complex multiphysics nature of the LMD technology that involves particle transportation, multiple flow interaction, particles-gas interaction with the energy source, and material phase-change. In particular, this work focuses on CFD (Computational Fluid Dynamics) simulations of the particle flow problem, regarding the coupling between a fluid phase, the carrier gas (Nitrogen), and a solid phase, i.e., a metallic material powder (e.g., 316L Stainless Steel) that is delivered through the nozzle of the LMD 3D printer.
Two different methodological approaches are investigated: (i) the first based on an Eulerian method to describe the carrier gas flow combined with a Lagrangian method to describe the particle flow and (ii) the second based on a pure Eulerian method to describe both the carrier gas flow and the particle flow. This research compares the two methods in terms of computational efficiency, implementation, and physical applicability.
The group, composed by Ing. Mauro Murer, Prof. Giovanni Formica, Dr. Simone Morganti, and Prof. Ferdinando Auricchio, is working on this activities within the MADE4LO project, funded by Regione Lombardia within the POR-FESR 2014-2020 program.
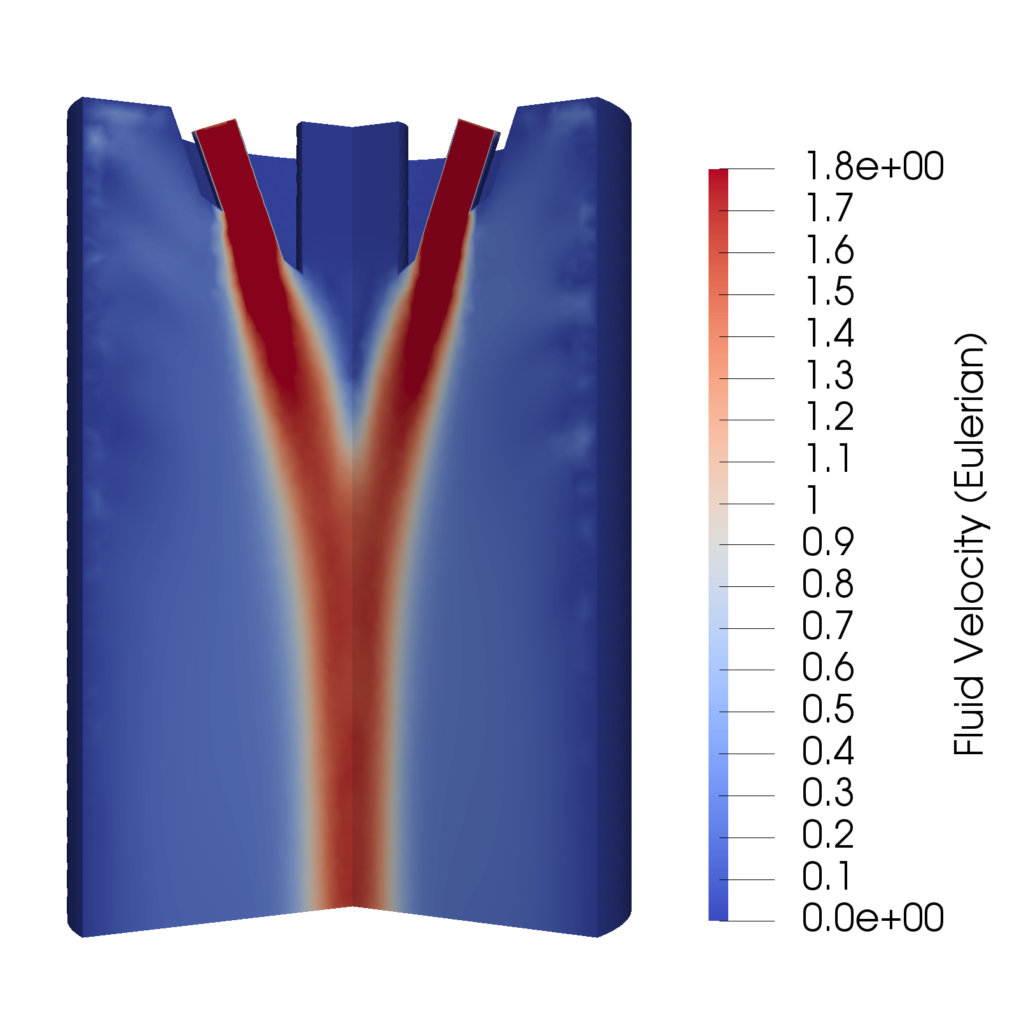
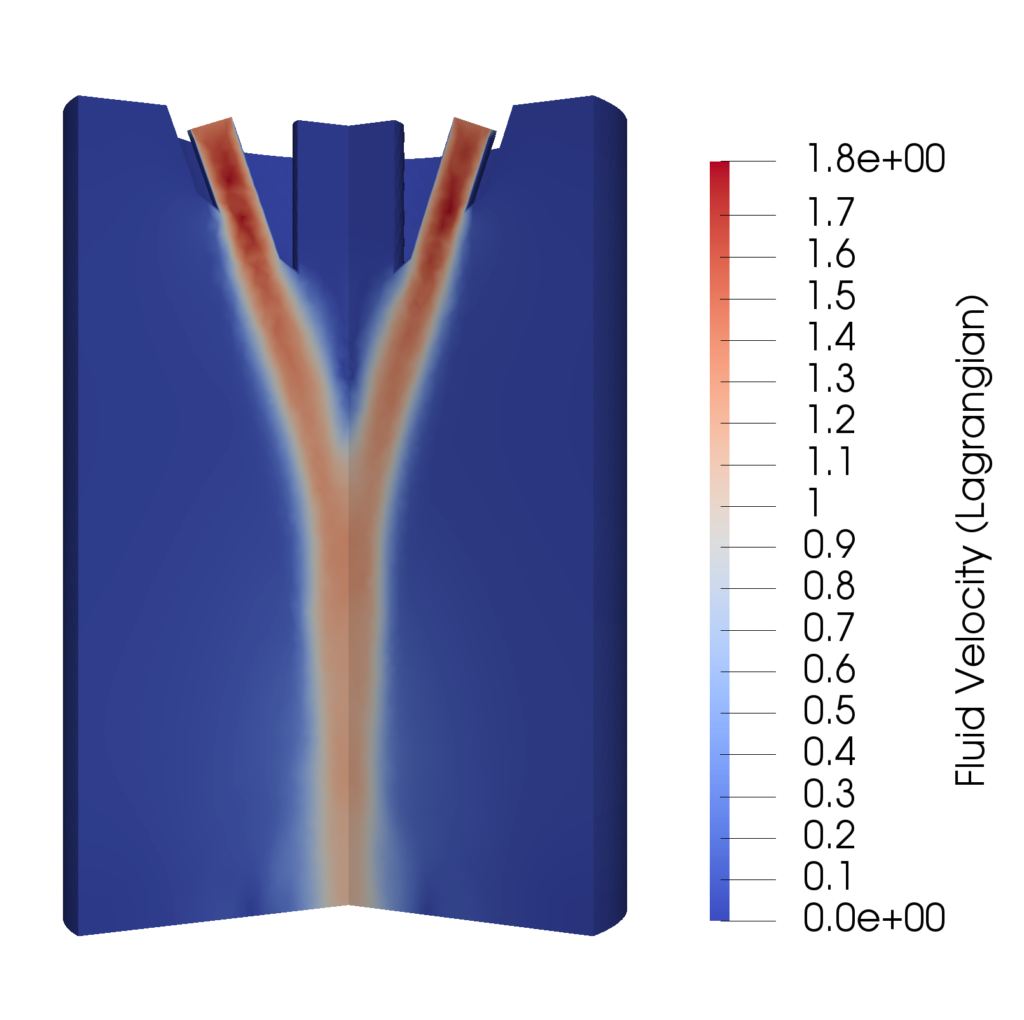
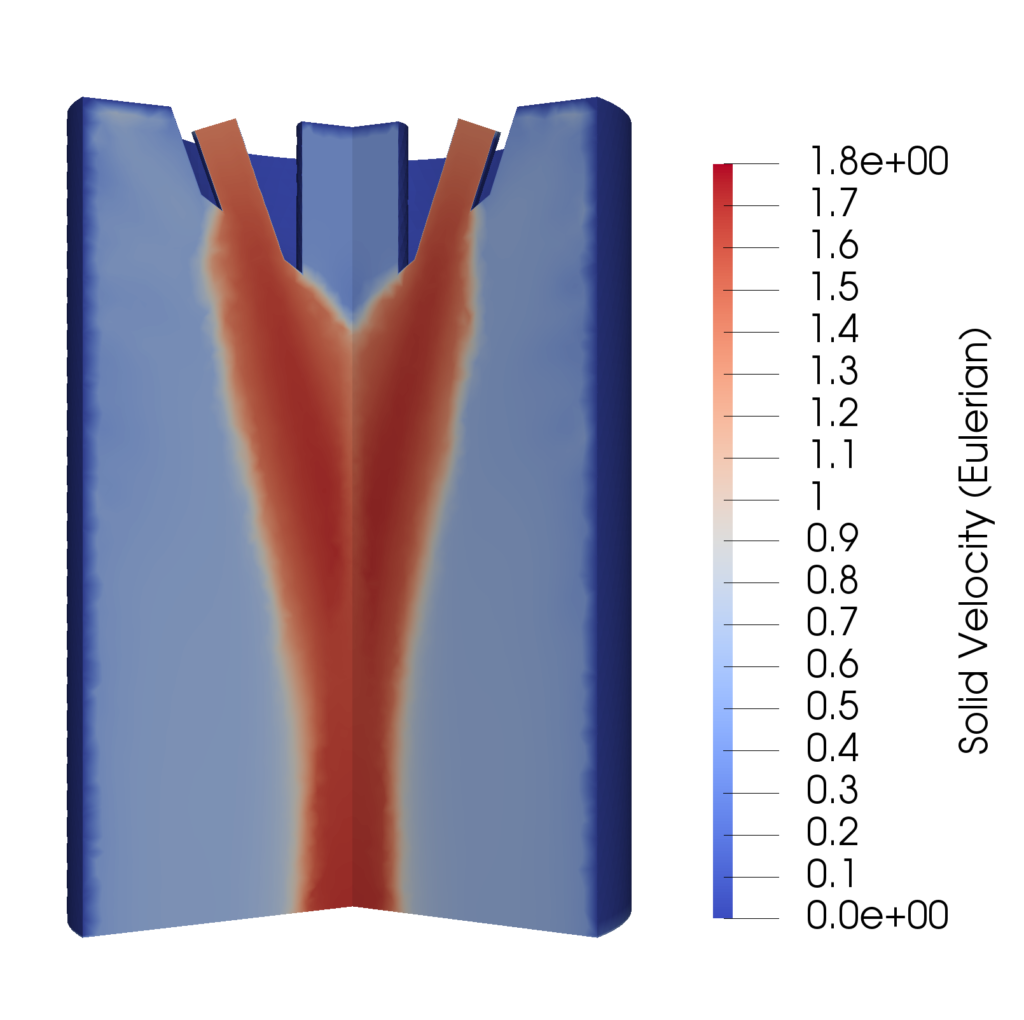
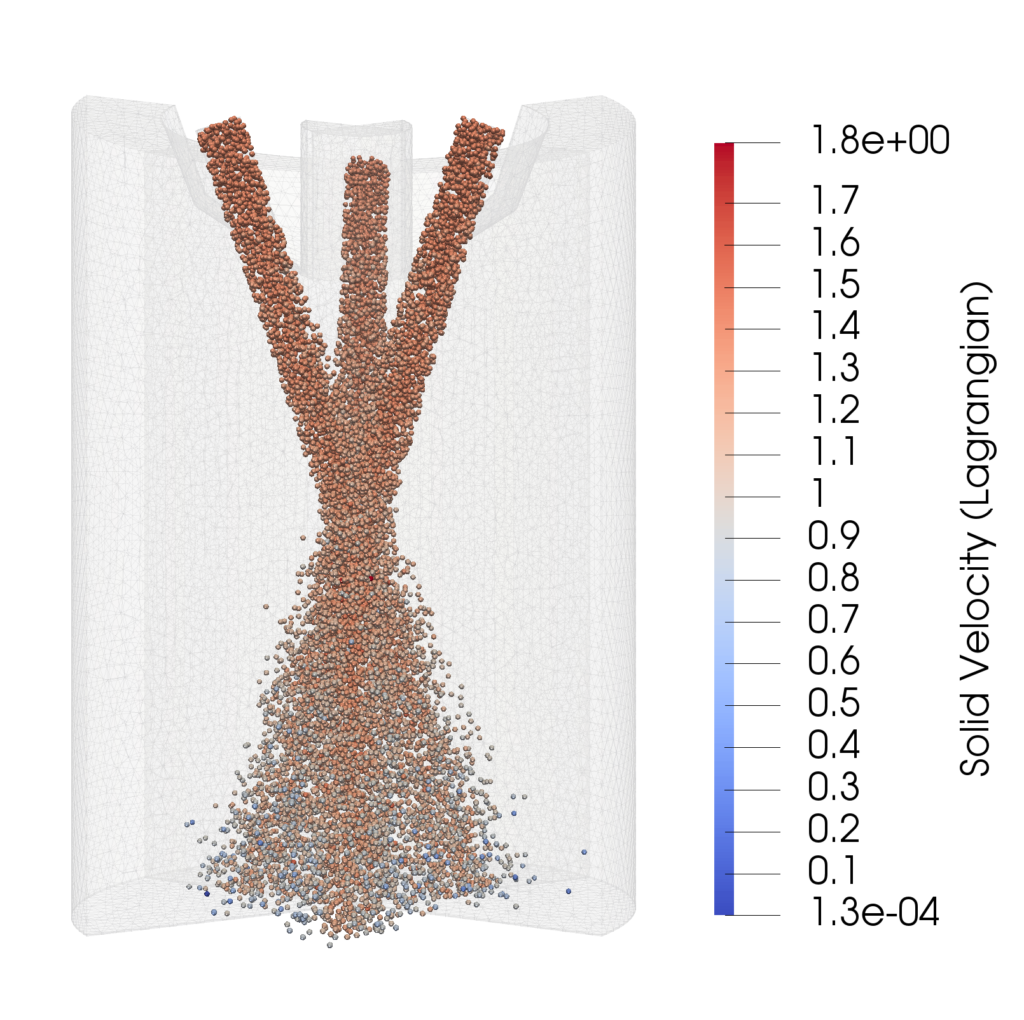
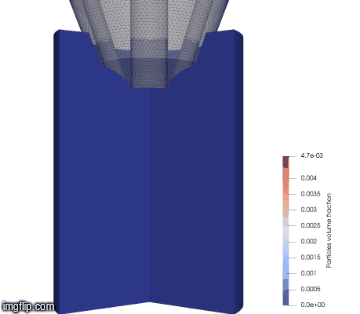
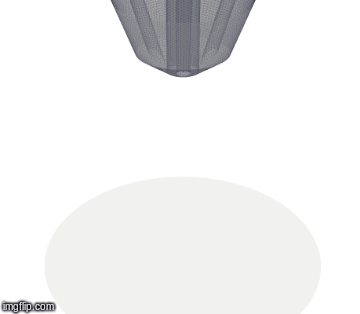
April 8th, 2019