Introduction
In common practice, it’s difficult to predict how the 3D printed material reacts to stresses. Correct Elastic Parameters are found through experimental tests.
ABS printed with Fused Deposition Modeling technology can be studied analytically, managing to characterize the sample without performing continuous tests.
Idea
The formation of the bonding in the FDM process is driven by the thermal energy of the semi-molten material.
The idea is to characterize this process, from micro level: analyzing the adhesion between the adjacent filaments and adhesion of a layer on the other, to macro level: analyzing the behaviour of the layer forming the equivalent homogeneous solid as orthotropic plates.
Thus, at macro level, the properties are referred to laminated sheets glued. On a micro level, the properties of each lamina are functions of the filaments properties, the bonds quality between the filaments, and the density of voids.
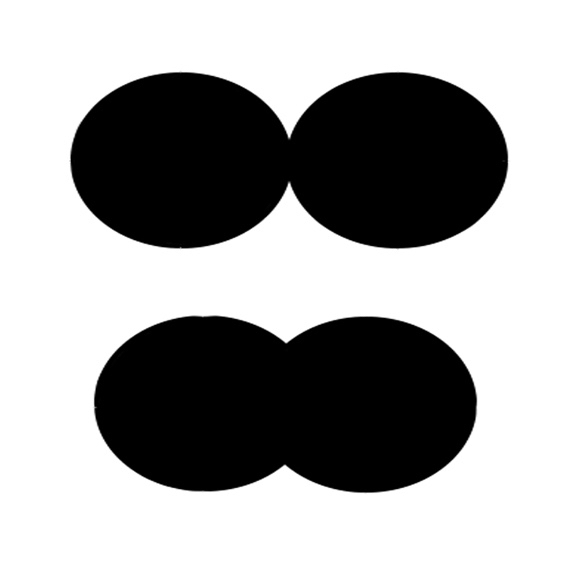
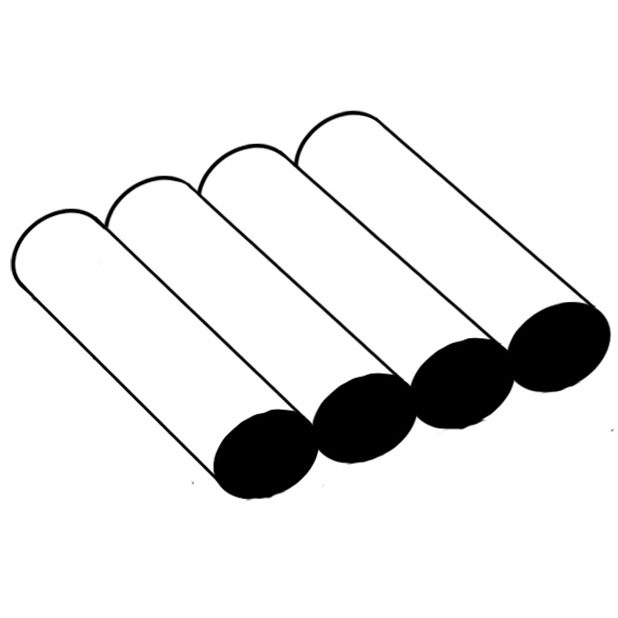
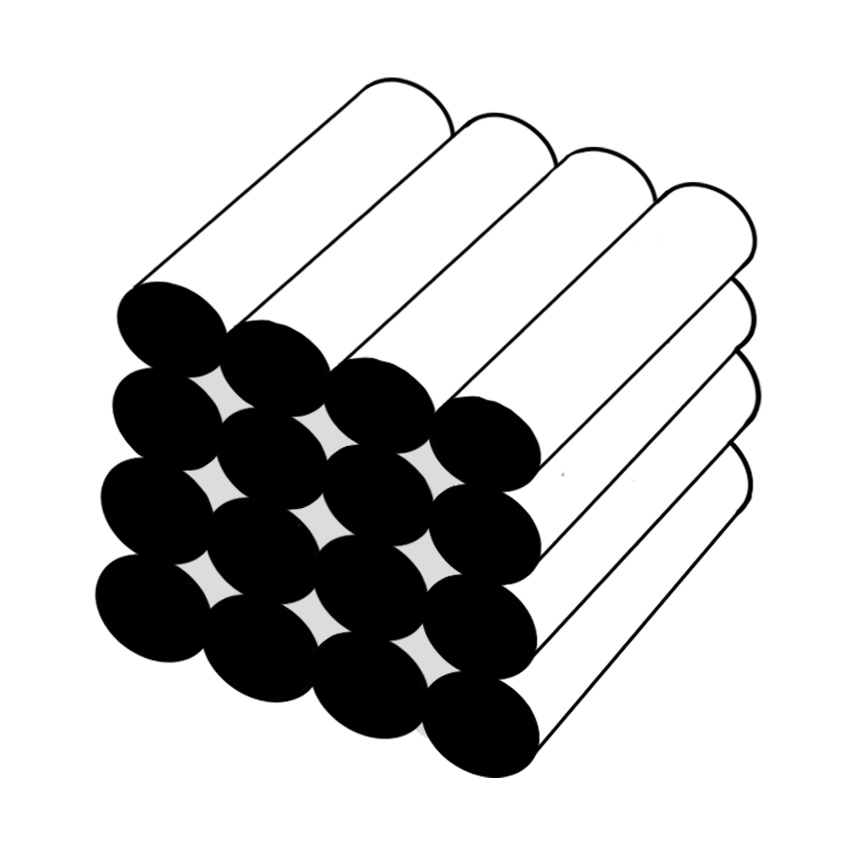
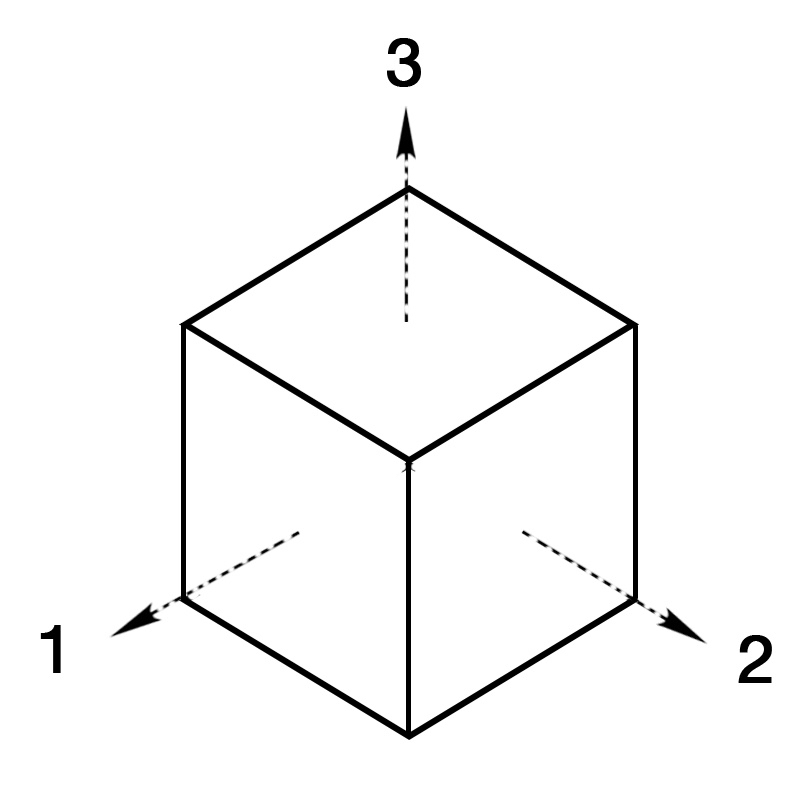
Fusion deposition process has been divided in three major parts:
- Sintering Process: the adhesion of two adjacent filaments.
- Thermal Analysis: It provides the temperature window in which the sintering phenomenon occurs.
- Lamination Analysis: the final stage aim to characterize the heterogeneous material as an homogeneous equivalent with elastic parameters reduced in function of the voids density.
Goal
The goal is to predict what will be the elastic parameters characterizing our specimens, in order to choose and predict the characteristics that we want to give to our printed material.
The prediction of Elastic Modulus leads to an optimized plot, and consequently, to save material and to make optimized form, maintaining adeguate mechanical properties.