We regard the numerical simulation of a microfluidic valve where liquid water interacts with a thin, lightweight membrane of similar densities in a nearly-enclosed fluid domain using the partitioned fluid-structure interaction (FSI) approach. The valve under investigation is an innovative micro-scale proportional valve designed by our industrial partner Dolphin Fluidics. It consists of two different but interdependent actuation types. A shape-memory alloy actuator controls the pilot chamber. The pressure change in the pilot chamber controls the deformation of the central membrane. The particularity of the device pertains to its ability to prevent any flow leakage while handling high-pressure differences ranging from 0.2 bar to 5 bars. However, although it is designed to provide accurate and proportionally variable flowrate, experiments showed that the valve has issues while partially open. Mainly, excessive vibrations occur when the valve is 30% partially open and manifest as noise due to rapid main membrane fluctuations. In addition, undesired turbulent flow is observed across the outlet. This behavior should be well understood to execute the appropriate changes in the valve design.
In this context, Ansys Multiphysics is used to simulate the coupled problem. The structural model is implemented in Ansys Mechanical, the fluid model is developed within Ansys Fluent, and the coupling is executed through Ansys SystemCoupling.
We control the pressure in the pilot chamber using a one-way FSI approach. The mechanical response and the fluid system are modeled using a two-way FSI approach. The quasi-Newton inverse least squares (IQN-ILS) stabilization method reduces the added-mass effect in this coupled problem and enhances the convergence behavior. The opening time duration up to 100% open setpoint equals 0.2 [sec]. The simulation uses a synchronized time-step size equal to 1e-5 [sec] and runs until a 50% partially open valve setpoint is reached, enough for observing the vibrations and investigating the flow behavior. The simulation runs to completion in around 253 hours on 64 AMD EPYC cores using Ansys HPC capabilities. The obtained results enable a better understanding of the valve operating system and will be used to improve the product design.
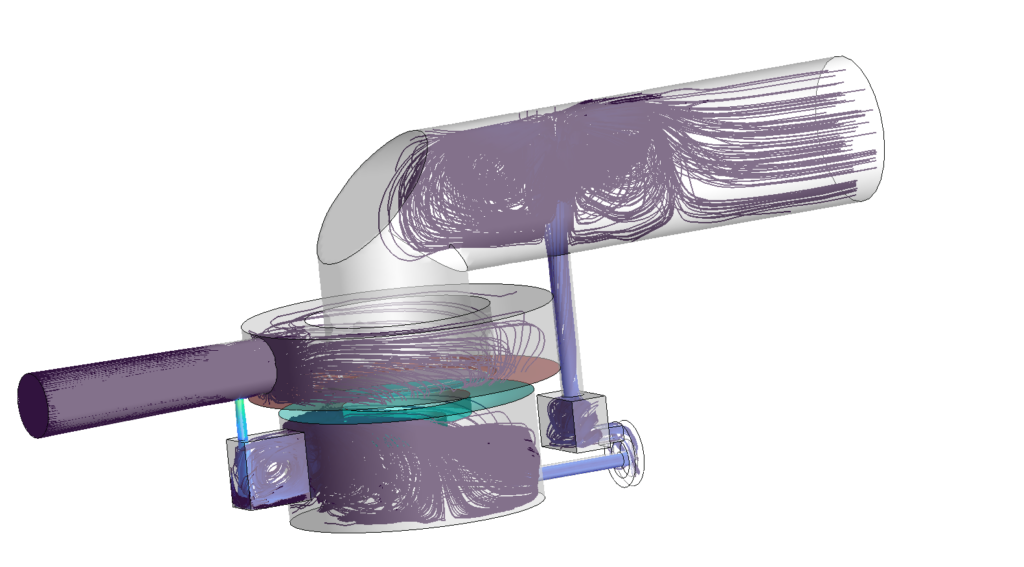
Fig. 1: Fluid velocity streamlines and membrane deformation at time t=0.06sec
June 1, 2022