Investigation of frequency-dependent temperature field of 3D-printed polyether ether ketone (PEEK) during fatiguetesting
During fatigue tests, PEEK specimens are subjected to cyclic stresses that cause internal energy dissipation which, in turn, results in a temperature increase. The higher the test frequency, the higher the temperature rise. This temperature increase can alter mechanical and physical properties, leading to reduced stiffness and strength and misleading measures. Moreover, fatigue tests could require a long time to be completed, therefore a tradeoff between test frequency and temperature increase is required.
Goal: measure the surface temperature of 3D-printed specimens during fatigue tests and ensure that it remains well below the glass transition temperature (Tg) of PEEK, which is 143°C.
Methods: fatigue specimens were subjected to cyclic force-controlled tests, to analyze the influence of frequency on the temperature increase. The force ranged from a minimum of 0N to a maximum of 1100 N, with frequencies of 2Hz, 5Hz, and 8Hz. A total of 15000 cycles was performed for each frequency since preliminary experiments have shown that beyond such a limit, the temperature reaches stationarity. The specimens were manufactured by an Apium P220 3D-printer, according to ASTM D638 type IV geometry (Fig. 1).
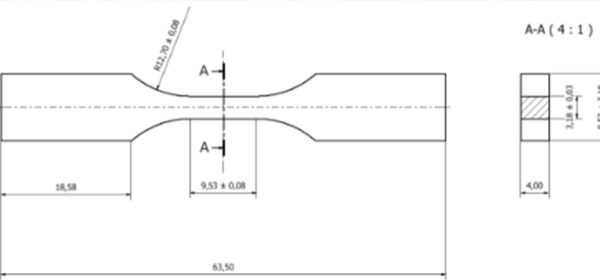
Figure 1: geometry of the specimen according to ASTM D638 standard test method
A FLIR A70 infrared thermal camera (Fig. 2) was used to monitor the real-time temperature field on the samples. The IFOV value of the FLIR A70 is compatible with the measurement distance.
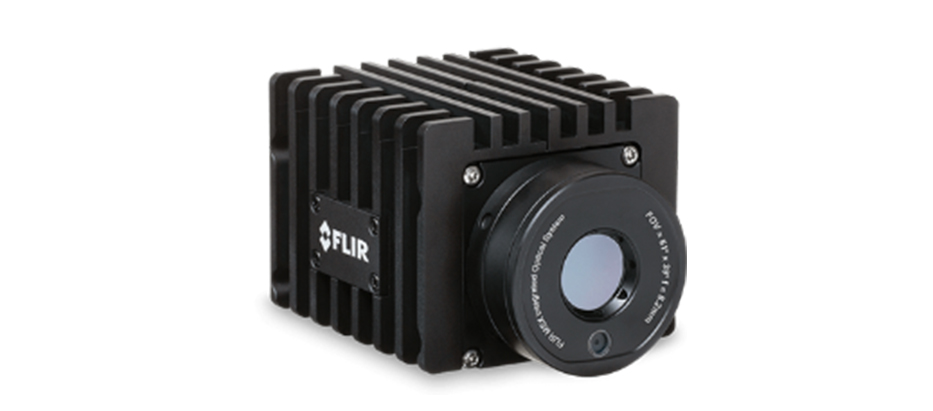
Figure 2: thermal camera FLIR A70
To ensure reliable temperature measurements, the emissivity (ε = 0.94, experimentally measured according to ISO 18434-1), the ambient temperature (24°C), and the distance between the thermal camera and the sample (0.5 m) were set in the camera software. An example of the experimental setup is shown in Fig. 3.
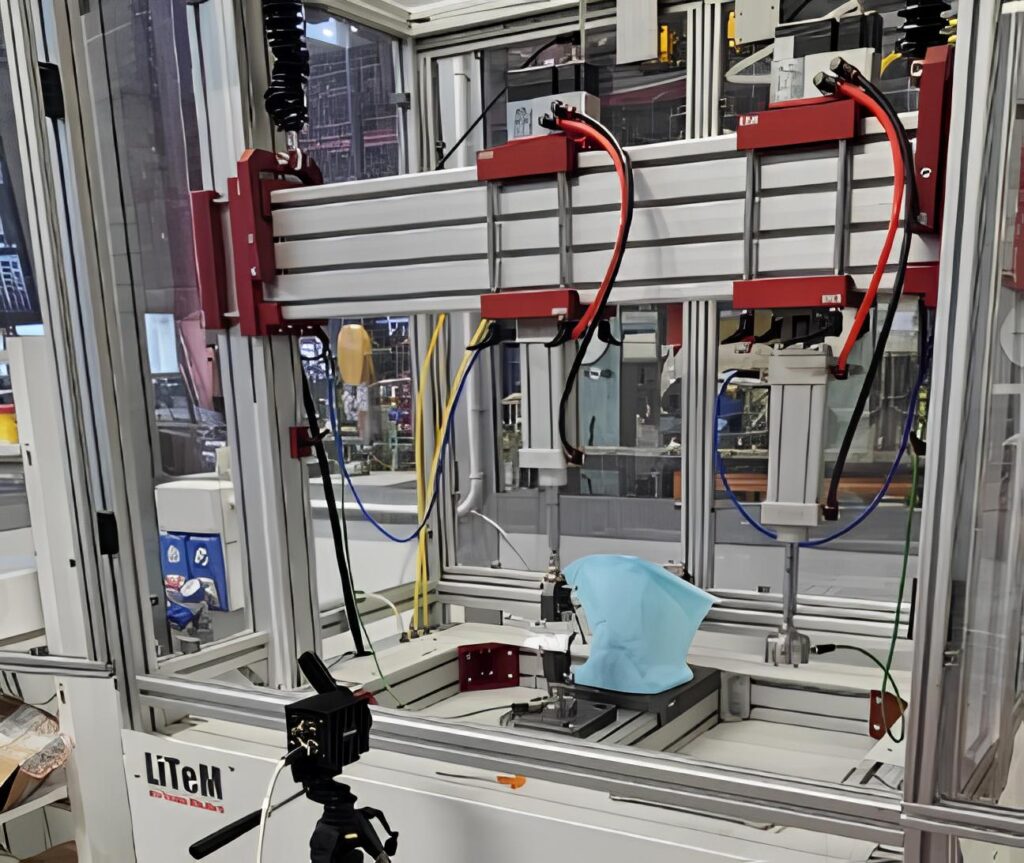
Figure 3: test set-up
Results: The full-field temperature analysis after 15000 cycles reported an increase, with respect to the ambient temperature (24°C), of 3°C for specimens tested at a frequency of 2Hz, an increase of 5°C at 5Hz, and an increase of 10°C at 8Hz (see Fig. 4, Fig. 5, and Fig. 6, respectively). Results prove that the thermal increase does not affect the mechanical and physical properties of PEEK during fatigue tests, given its Tg of 143°C
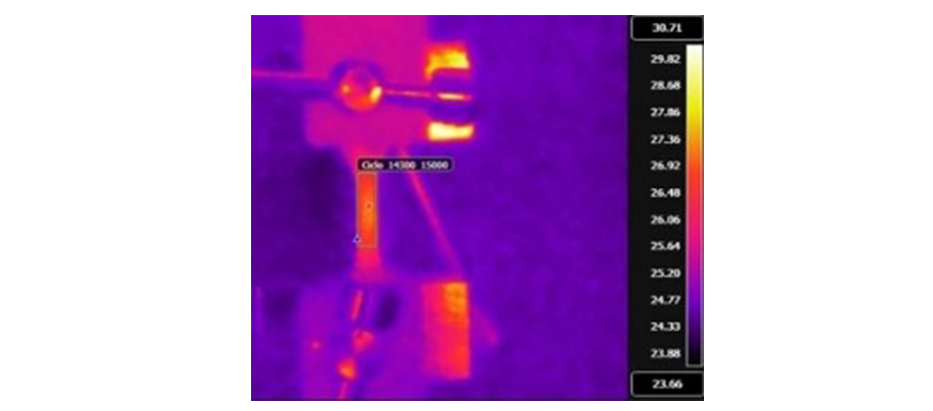
Figure 4 – 2Hz frequency: temperature field after 15000 cycles, with an average increase of about 3°C with respect to ambient temperature (24°C).
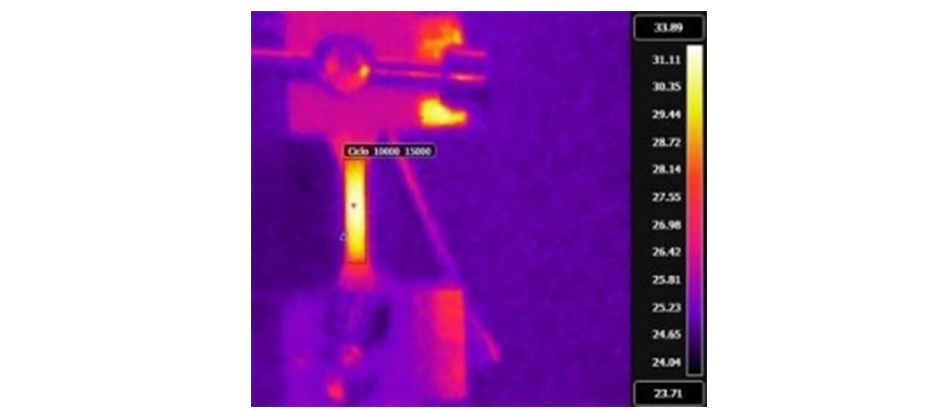
Figure 5 – 5Hz: temperature field after 15000 cycles, with an average increase of about 5°C with respect to ambient temperature (24°C).
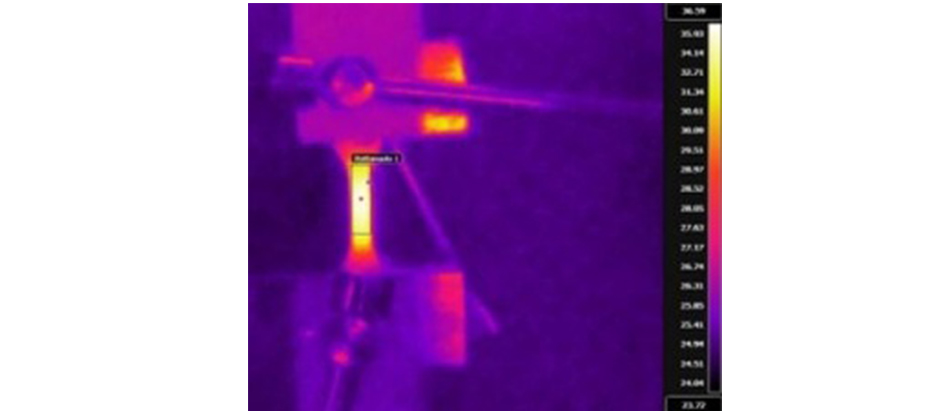
Figure 6 – 8Hz frequency: temperature field after 15000 cycles, with an average increase of about 10°C with respect to ambient temperature (24°C).
Credits: the analysis was conducted by L. Ruccolo, G. Zanellati, and B. Rossetti using the Litem BYC 200 machine available at the Department of Civil Engineering and Architecture (DICAR) of Pavia University. 3D-printing specimens’ profile was developed with the support of S. Serioli and F. Rotini. The activity was supervised by S. Marconi and F. Auricchio and managed by G. Alaimo.