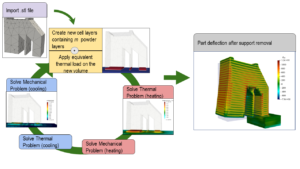
The capability to correctly predict part deflections after support removal is important to assess the quality of the final artifact produced by laser powder bed fusion (LPBF) technology.
Finite Element Methods (FEM) are usually employed to perform part-scale thermo-mechanical analysis to estimate the final distortion of components. A simple yet effective physical model is the so-called pragmatic approach, which sequentially activates blocks of material at melting temperature, predicting part deflections with good accuracy.
Besides an effective physical model, another key issue in LPBF part-scale simulations is the complexity of the geometrical parts typically involved in this kind of analysis. Classical FEM-based approaches require a conforming mesh generation process, which, for complex, optimized geometries, can be very time-consuming.
Immersed boundary methods represent an attractive way to effectively handle the numerical analysis of complex geometrical components. In particular, the Finite Cell Method (FCM) has been already applied to simulate thermal and thermo-mechanical problems of both welding and additive manufacturing processes. However, for LPBF processes, these studies were limited to small length-scales of approximately 1 mm3.
With this project, we aim at developing an immersed numerical framework, based on the FCM concept, suitable to effectively simulate an LPBF process directly from the original geometry (in the .stl file format). Its main feature is a fully automatic and straight-forward discretization process that can be readily applied to complex geometries, the so-called AM design-through-analysis depicted in Fig. 1.
The numerical results obtained so far show the effectiveness of the proposed numerical method, which is able to deliver solutions in excellent agreement with experimental measurements. The project is carried out together with the researchers of the group of Simulation in Applied Mechanics (John Jomo, M.Sc. and Dr. Stefan Kollmannsberger) of the Technical University of Munich (TUM). The results are obtained employing AdhoC++, an in-house software developed and maintained at the Chair of Computation in Engineering (Prof. Ernst Rank).
April 10th, 2020