Prof. Dr.-Ing. Julia Mergheim
Institute of Applied Mechanics
Department of Mechanical Engineering
Friedrich-Alexander-Universität Erlangen-Nürnberg
June 8, 2021 – 11.00 am (CEST)
Zoom Meeting
https://us02web.zoom.us/j/84764644341?pwd=a2FLM1Yzdk1oNHFVS1loS29OUXJBdz09
Meeting ID: 847 6464 4341
Passcode: 301645
YouTube Live channel
https://www.youtube.com/channel/UCbuPu16F7DAuqSEX63agXyA
Selective laser or electron beam melting are additive manufacturing processes that start with a powder-bed and generate the desired part by selectively melting the powder layer-by-layer. After solidification, the solid part geometry is obtained. These additive manufacturing processes make it possible to create various complex geometries, but can also produce different material properties, depending on the process parameters.
In this presentation, a combination of simulation methods – macroscopic, mesoscopic and numerical homogenization – will be presented to relate the properties of the resulting material to the process strategy. A macroscopic thermo-mechanical Finite Element (FE) process simulation is introduced and thoroughly analyzed. The adaptive FE-solver is based on the open source FE library deal.ii and makes use of heavy parallelization. A detailed numerical analysis of various assumptions from the literature is performed. The influences of a geometrically linear or nonlinear setting, stress relaxation or the surrounding powder are examined. Furthermore, recommendations for simulation parameters such as element type, mesh size and time step size are given.
The simulated macroscopic temperature field is then used as input for a cellular automaton to simulate the evolving grain structure. Examples for Nickel alloys are given and validated by experimental results.
Finally, the macroscopic mechanical properties of the resulting grain structure are derived by means of numerical homogenization, using a gradient-enhanced crystal plasticity model on the mesoscopic scale. Representative Volume Elements are constructed with the grain structure output from the cellular automaton simulation. The macroscopic elastic and plastic material behavior of a Nickel alloy are identified and validated by experimental results.
Biography: Julia Mergheim is Professor for Applied Mechanics at the Friedrich-Alexander-Universität Erlangen-Nürnberg. Her work focuses on numerical mechanics, fracture and damage mechanics, material mechanics and numerical homogenization, and simulation of additive manufacturing processes.
Prof. Mergheim received her Diploma in Civil Engineering from the Ruhr-University in Bochum in 2002 and her PhD in Mechanics from the University of Kaiserslautern in 2005. She spent some time in industrial research before returning to the University in Kaiserslautern as an assistant professor in 2007. Since 2009, she has been researching and teaching at the FAU Erlangen-Nürnberg. Prof. Mergheim is currently supervising six PhD students and several Master students. She is principal investigator in the Research Training Groups Fracture across Scales and Energy Conversion Systems: From Materials to Devices and, since 2011, in the Collaborative Research Center 814 Additive Manufacturing.
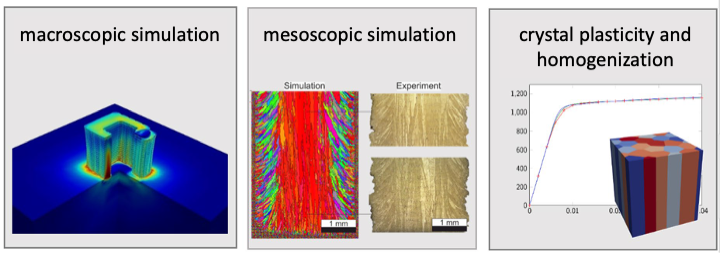