Several concepts have been developed for actuation of microvalves in order to fulfill multiple desired characteristics such as the reduction of flow leakage and power consumption, improved response time, high work density and the ability to operate with both liquids and gases [1]. Shape memory alloys (SMA) are a class of smart materials operating with thermal microvalves type. The advanced technology allows for simple and compact structures with high output forces and can control high-pressure differences [2-3].
We aim to present an introduction to micro-scale valves, their advantages, and a review of the shape memory alloys (SMA) microvalve designed by Dolphin Fluidics.
We will present relevant methodologies and techniques to study the microvalve model developed by Dolphin Fluidics, several computational fluid dynamics (CFD) simulations to describe the fluid behavior during valve opening/closing phases. Finite Volume Method (FVM) is used to discretize the model through ANSYS Fluent solver to study the fluid behavior, including pressure differences, velocity, and forces at boundaries. The preliminary analysis and results discussed may be useful for future optimization processes.
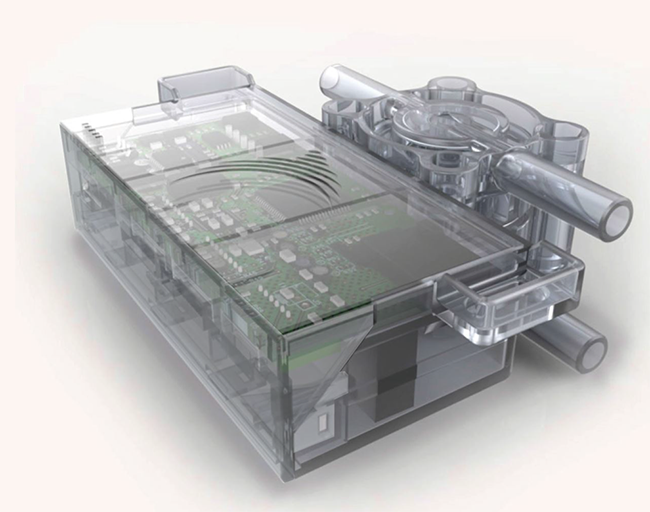
References:
[1] Oh, Kwang W Oh, and Chong H Ahn. “A review of microvalves.” Journal of micromechanics and microengineering 16.5 (2006): R13-R39.
[2] Kohl, et al. “Development of stress-optimised shape memory microvalves.” Sensors and actuators. A, Physical 72.3 (1999): 243-250.
[3] Megnin, Christof Megnin, and Manfred C Kohl. “Shape memory alloy microvalves for a fluidic control system.” Journal of micromechanics and microengineering 24.2 (2014):025001. O.C.
March 18th, 2019