FATIGUE TEST AND WEAR ASSESSMENT ON 3D PRINTED TPU SPECIMENS
The test has been carried out by the ProtoLab members B. Rossetti and L. Montaldo using the Litem BYC 200 machine, available at the Department of Civil Engineering and Architecture (DICAR) of Pavia University.
The research activity has been supervised and designed by G. Alaimo, S. Marconi and F. Auricchio.
A displacement-controlled fatigue test was performed to evaluate the wear of 3D printed TPU (thermoplastic polyurethane) cubes with gyroid structure (Fig.1).
The goal was to test the long-term integrity of additively manufactured specimens by analyzing their response in terms of maximum and minimum loads.
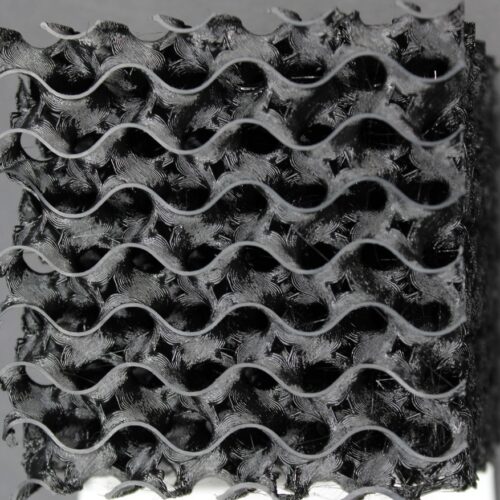
Figure 1: Thermoplastic polyuretane gyroid cube
Specimens were subjected to compression cyclic test, deforming them within a range of 10mm to 50mm at a frequency of 2 Hz, for a total number of 150’000 cycles.
Every 50’000 cycles, the test was paused to check for any macroscopic damage, acquiring detailed images of the specimens. Minimum and maximum load values, observed at the respective displacement values of 10mm and 50mm, were recorded every 100 cycles.
From the analysis of the data (Fig.2), it is observed that the load loss percentage turned out to be 4% every 100’000 cycles.
Moreover, the comparison of the specimen images at the beginning and at the end of the test showed that there are no evident macroscopic damages either. This result highlights the value of experimental test to assess and validate both wearing and fatigue life estimation also on non convectional structures.
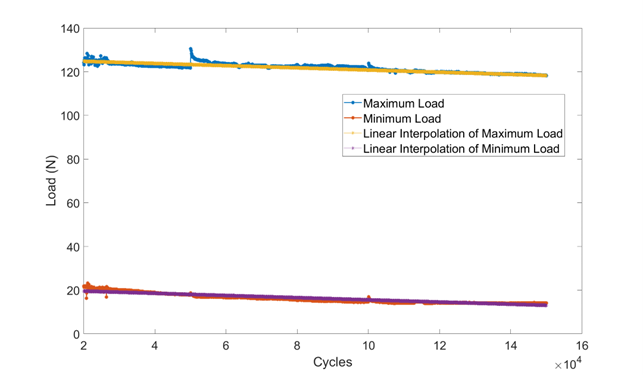
Figure 2 Maximum and miminum loads vs the number of cycles, along with their linear interpolation.