Fused Filament Fabrication (FFF), although introduced for rapid-prototyping applications, has outgrown its intended purpose. With the availability of high-performance materials and the high-level control of the process, FFF is now being explored for its potential to fulfil the industry manufacturing needs. However, some limitations in the exploitation of FFF technology still exist. For example, the deposition paths used to fill the geometry to be printed can follow only certain defined patterns implemented in the current slicing software (rectilinear, honeycomb, concentric etc.), thus preventing an enhanced deposition strategy of the material. The inherent anisotropic nature of the 3D-printed parts along with such predefined patterns may not result in desirable structural performance for most applications. Hence a load-oriented filament deposition is used.
The present work makes a step forward developing a robust, generally valid deposition technique for any two-dimensional structural application. The algorithm currently in development could generate paths allowing for a user-specified overlap to occur and fills relatively large voids in between the filaments.
Acknowledgement:
This project has received funding from the European Union’s Horizon 2020 programme under the Marie Sklodowska-Curie Innovative Training Networks European Joint Doctorate (Grant Agreement No 764736).
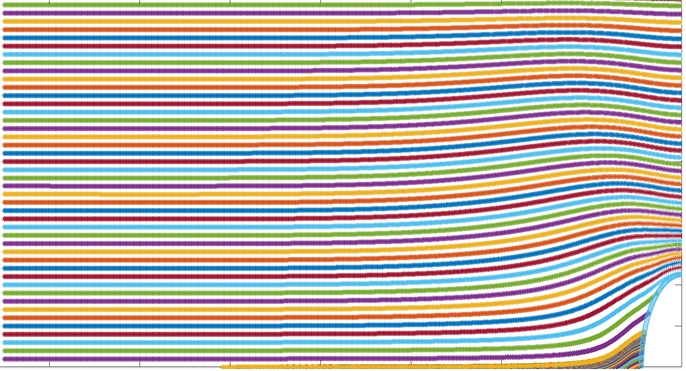
Fig. 1 Filament Path for One-Quater of a plate with a hole
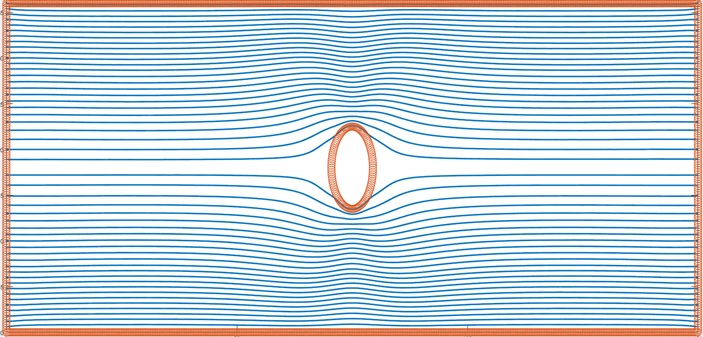
Fig. 2 Curvilinear Filament path deposition
April 15th, 2019